Semiconductor Silicon Wafer Testing Machine | SEMISHARE
SEMISHARE presents the latest trends in semiconductor silicon wafer testing machine technology. Stay ahead in the evolving silicon wafer testing landscape.
SEMISHARE: Advancing Semiconductor Wafer Testing Technology
In the rapidly evolving world of semiconductor manufacturing, the need for precise and reliable wafer testing has never been more critical. SEMISHARE, a leading innovator in semiconductor wafer test technology, is at the forefront of this industry, providing cutting-edge solutions for silicon wafer testing, wafer test procedures, and advanced wafer testing machines. Our commitment to excellence and innovation has positioned us as a trusted partner for semiconductor manufacturers worldwide.
The Importance of Semiconductor Wafer Testing
Semiconductor wafer test is a crucial step in the manufacturing process, ensuring the quality and functionality of integrated circuits before they are cut into individual chips. As the complexity of semiconductor devices continues to increase, the role of wafer testers becomes increasingly vital. SEMISHARE's advanced wafer testing machines are designed to meet these evolving challenges, providing accurate and efficient testing solutions.
Silicon wafer testing is not just about identifying defects; it's about ensuring the overall quality and performance of the semiconductor devices. Our wafer test solutions are designed to provide comprehensive data on various parameters, enabling manufacturers to optimize their processes and improve yield.
How Do You Test a Wafer?
The process of wafer test involves several key steps:
1. Wafer Placement: The silicon wafer is carefully positioned on the wafer testing machine.
2. Probe Alignment: Microscopic probes are aligned with specific test points on the wafer.
3. Electrical Testing: The wafer tester applies electrical signals and measures the responses.
4. Data Analysis: The collected data is analyzed to assess the wafer's performance and identify any defects.
5. Mapping: A wafer map is created to indicate the location of functional and non-functional dies.
SEMISHARE's wafer testers are equipped with advanced automation features that streamline this process, ensuring high accuracy and efficiency in semiconductor wafer testing. Our wafer testing machines are designed to handle a high volume of tests while maintaining precision and reliability.
What is the Test of Silicon Wafers?
Silicon wafer testing involves a comprehensive evaluation of the wafer's electrical and physical properties. This includes:
1. Parametric Testing: Measuring electrical parameters such as resistance, capacitance, and current leakage.
2. Functional Testing: Verifying the proper operation of integrated circuits on the wafer.
3. Reliability Testing: Assessing the wafer's performance under various stress conditions.
4. Physical Inspection: Examining the wafer for surface defects or irregularities.
SEMISHARE's wafer testing machines are designed to perform all these tests with high precision, ensuring thorough quality control in the semiconductor manufacturing process. Our silicon wafer testing solutions provide manufacturers with detailed insights into wafer quality, helping to identify and address potential issues early in the production process.
How Are Semiconductor Wafers Measured?
Semiconductor wafers are measured using a combination of electrical and optical techniques. SEMISHARE's wafer testers employ advanced measurement technologies, including:
1. Four-Point Probe Method: For measuring sheet resistance and resistivity.
2. Capacitance-Voltage (C-V) Measurements: To evaluate semiconductor properties and oxide quality.
3. Current-Voltage (I-V) Characterization: For assessing device performance and reliability.
4. Optical Metrology: To measure physical dimensions and detect surface defects.
These measurement techniques, integrated into our wafer testing machines, provide comprehensive data on wafer quality and performance. Our wafer test solutions offer high-precision measurements, enabling manufacturers to maintain strict quality control standards.
What is a Wafer Prober?
A wafer prober is a key component of the wafer testing process. It is responsible for precisely positioning the wafer and aligning the test probes with specific points on the wafer's surface. SEMISHARE's wafer probers are designed for high accuracy and reliability, featuring:
1. Automated Alignment Systems: For precise probe-to-pad contact.
2. Multi-Axis Positioning: Allowing for testing of complex wafer designs.
3. Temperature Control: To simulate various operating conditions during testing.
4. Integration with Test Equipment: For seamless data collection and analysis.
Our wafer probers are an integral part of our comprehensive wafer testing solutions, ensuring efficient and accurate semiconductor wafer testing. The precision of our wafer probers contributes significantly to the overall accuracy of the wafer test process.
The Wafer Testing Process
The process of wafer probing is a critical step in semiconductor manufacturing. SEMISHARE's wafer testing machines are designed to optimize this process:
1. Wafer Loading: Automated systems carefully load the wafer onto the prober.
2. Alignment: Advanced optical systems ensure precise alignment of probes with test points.
3. Testing Sequence: Programmable test sequences allow for comprehensive wafer evaluation.
4. Data Collection: Real-time data gathering and analysis for immediate quality assessment.
5. Wafer Mapping: Generation of detailed wafer maps for yield analysis and process improvement.
This streamlined process ensures thorough and efficient wafer testing, contributing to higher yields and better quality control in semiconductor manufacturing. Our wafer test solutions are designed to maximize throughput without compromising on accuracy.
Measuring Wafer Resistance
One crucial aspect of silicon wafer testing is measuring the wafer's resistance. SEMISHARE's wafer testers employ the four-point probe method for accurate resistance measurements:
1. Probe Placement: Four probes are placed in a line on the wafer's surface.
2. Current Application: A known current is passed through the outer probes.
3. Voltage Measurement: The voltage drop is measured between the inner probes.
4. Resistance Calculation: The wafer's sheet resistance is calculated using these measurements.
This method, integrated into our wafer testing machines, provides precise resistance data crucial for quality control and process optimization. Our silicon wafer testing equipment ensures highly accurate resistance measurements, contributing to the overall reliability of the semiconductor devices.
Wafer Test vs. Final Test
Understanding the difference between wafer test and final test is crucial in semiconductor manufacturing:
Wafer Test:
-
Performed on entire wafers before dicing.
-
Identifies defects early in the manufacturing process.
-
Enables wafer-level reliability testing and process monitoring.
Final Test:
-
Conducted on packaged chips after dicing and assembly.
-
Verifies functionality under final operating conditions.
-
Includes additional tests like burn-in and environmental stress screening.
SEMISHARE's wafer testing solutions are designed to optimize the wafer test phase, reducing costs and improving overall product quality. Our wafer testers provide comprehensive data that helps manufacturers make informed decisions about which dies to package and test further.
SEMISHARE's Advanced Wafer Testing Machines
SEMISHARE's wafer testing machines represent the cutting edge of semiconductor wafer test technology. Our systems offer:
1. High Precision: Sub-micron accuracy in probe positioning.
2. Automated Operation: 24/7 unattended testing capabilities.
3. Temperature Control: Wide range temperature testing from -60°C to 300°C.
4. Multi-Site Testing: Simultaneous testing of multiple dies for increased throughput.
5. Advanced Software: User-friendly interface with powerful analysis tools.
6. Customization: Tailored solutions for specific testing requirements.
These features make SEMISHARE's wafer testers ideal for a wide range of applications, from research and development to high-volume production testing. Our wafer testing machines are designed to meet the diverse needs of the semiconductor industry, providing flexible and scalable solutions.
Advantages of SEMISHARE's Wafer Test Solutions
1. High Accuracy: Our wafer testers provide precise measurements, ensuring reliable test results.
2. Increased Efficiency: Automated processes and multi-site testing capabilities improve throughput.
3. Versatility: Our wafer testing machines can handle a wide range of wafer sizes and types.
4. User-Friendly Interface: Intuitive software makes operation and data analysis straightforward.
5. Robust Design: Built to withstand continuous operation in demanding manufacturing environments.
6. Comprehensive Support: Our team of experts provides training and technical assistance.
These advantages make SEMISHARE a preferred choice for semiconductor manufacturers looking for reliable and efficient wafer test solutions.
The Future of Wafer Testing
As semiconductor technology continues to advance, wafer testing techniques must evolve to meet new challenges. SEMISHARE is committed to staying at the forefront of this evolution:
1. AI and Machine Learning Integration: Enhancing defect detection and classification.
2. 3D IC Testing: Developing solutions for testing complex three-dimensional integrated circuits.
3. Increased Parallelism: Improving throughput with multi-site and multi-wafer testing capabilities.
4. Advanced Materials Testing: Adapting to new semiconductor materials beyond silicon.
5. Nano-scale Probing: Developing ultra-fine probes for testing increasingly smaller features.
SEMISHARE's ongoing research and development ensure that our wafer testing solutions remain at the cutting edge of technology. We continually update our wafer testers and wafer testing machines to meet the evolving needs of the semiconductor industry.
Applications of SEMISHARE's Wafer Test Solutions
Our wafer testing machines find applications in various sectors of the semiconductor industry:
1. Foundries: For process control and yield optimization.
2. IDMs: For product development and quality assurance.
3. OSAT Companies: For wafer-level testing and packaging.
4. Research Institutions: For advanced semiconductor research and development.
Each of these sectors benefits from the precision, reliability, and efficiency of SEMISHARE's wafer test solutions.
Customer Success Stories
Many leading semiconductor companies have benefited from SEMISHARE's wafer testing solutions. For example, a major foundry was able to increase its testing throughput by 30% after implementing our advanced wafer testers. Another customer, a research institution, praised the flexibility and accuracy of our wafer testing machines in their cutting-edge semiconductor research.
These success stories highlight the real-world impact of SEMISHARE's commitment to innovation in semiconductor wafer test technology.
SEMISHARE's Commitment to Quality
At SEMISHARE, quality is at the heart of everything we do. Our wafer testing machines undergo rigorous quality control processes to ensure they meet the highest standards of performance and reliability. We adhere to international quality management standards and continuously improve our processes to deliver the best possible products to our customers.
Global Support and Services
SEMISHARE provides comprehensive support services to ensure our customers get the most out of their wafer test equipment:
1. Installation and Training: Expert installation and user training for optimal system performance.
2. Technical Support: Responsive technical assistance to address any issues promptly.
3. Maintenance Services: Regular maintenance to ensure long-term reliability of wafer testers.
4. Software Updates: Regular updates to enhance functionality and performance.
5. Customization Services: Tailored solutions to meet specific testing requirements.
Our global support network ensures that customers worldwide can rely on SEMISHARE for their wafer testing needs.
In the fast-paced world of semiconductor manufacturing, reliable and efficient wafer testing is crucial for maintaining quality and driving innovation. SEMISHARE's advanced semiconductor wafer test solutions, including our state-of-the-art silicon wafer testing equipment, wafer testers, and wafer testing machines, provide the precision and reliability needed to meet these challenges.
Our commitment to innovation, quality, and customer satisfaction has established SEMISHARE as a leader in the field of wafer testing. Whether you're involved in research and development, small-scale production, or high-volume manufacturing, SEMISHARE has the expertise and technology to support your semiconductor testing needs.
As we look to the future, SEMISHARE remains dedicated to advancing wafer test technology. We continue to invest in research and development, pushing the boundaries of what's possible in semiconductor wafer testing. Our goal is to provide our customers with the tools they need to stay competitive in an ever-evolving industry.
For more information about our wafer testing solutions or to discuss your specific requirements, visit our website at https://www.semishareprober.com/ or contact our sales team. Let SEMISHARE be your partner in advancing semiconductor technology through precision wafer testing. Together, we can shape the future of the semiconductor industry, one wafer at a time.
Driven by Moore's Law, integrated circuits are also greatly reducing circuit size, volume and cost, and continuously improving processing speed and performance. The continuous advancement of aerospace, the development trend of automobile electrification, and the arrival of the 5G era, how to ensure stable operation in various complex environments, all of which have put forward higher requirements for the new generation of integrated circuits, and wafer testing has also changed. It gets more complicated. As the amount of semiconductor investment continues to increase, the tolerance for design errors is almost zero, so strict verification tests must be carried out before the chip enters mass production and during mass production.
WAT (Wafer Acceptance Test) test is an important site for wafer manufacturing. It is used in conjunction with a probe station and a tester. It is used to test the testkey on the completed wafer for electrical testing. Generally, sampling tests are performed (5 points or more per wafer). If some important parameters do not meet the requirements, the wafer will be scrapped and will not enter the next stage. The WAT test reflects the stability of the wafer factory's processing technology.
CP (Chip Probing) test is used in conjunction with a probe station and an ATE tester to test the functions and electrical parameters of the chips on the wafer. The probe station is responsible for the transportation and positioning of the wafer, ensuring that the surface of the wafer is moved to the precision The instrument delivers a more stable signal, so that the Dies on the wafer are in contact with the probes and tested one by one (or in parallel) to achieve more accurate data testing and measurement. After the completion of the wafer production, due to various manufacturing defects introduced due to process reasons, there will be a certain amount of unqualified products in the Die distributed on the wafer. The purpose of CP testing is to find out these unqualified products before packaging. On the one hand, it analyzes the cause of failure, so as to increase the yield of the product subsequently, and on the other hand, reduce the cost of subsequent packaging and testing.
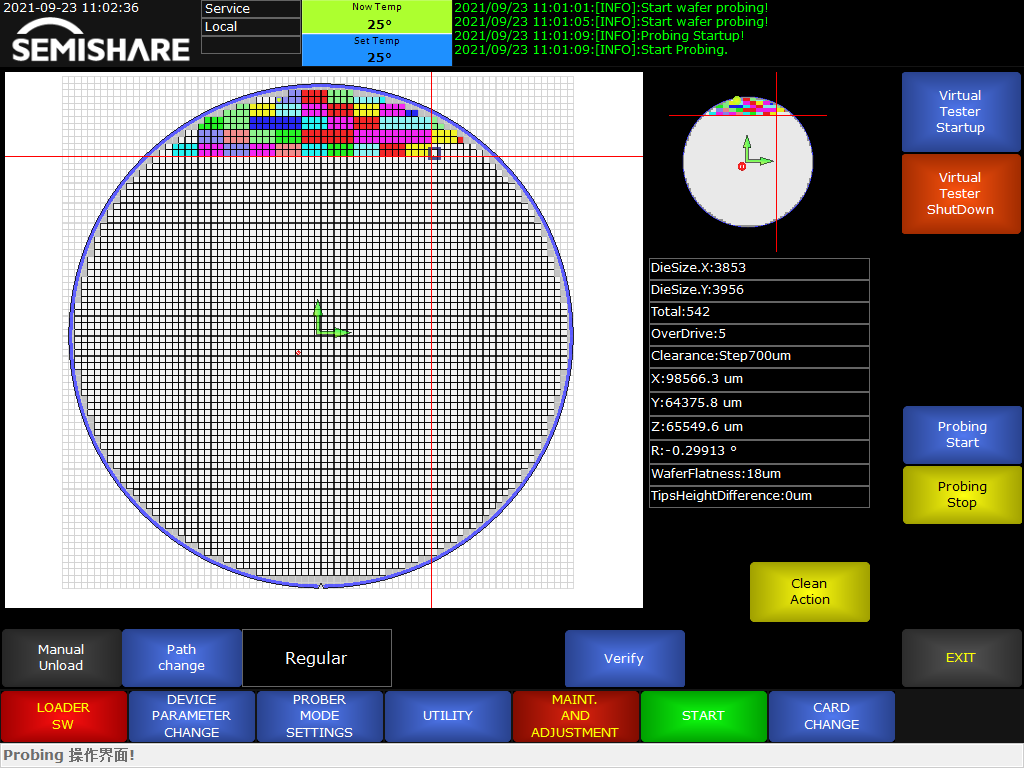
With the rapid development of global informatization, networking and knowledge economy, semiconductor products are also constantly undergoing innovation and technological iteration. The pressure from the market forces engineers and scientists to constantly update their technologies, reduce the time to market, and leave the wafer test time for fabs or laboratories more tight and precious. In the process of WAT test and CP test, how does the probe station, which plays an important role, meet the needs of engineers? SEMISHARE has intensively cultivated the probe station industry for more than ten years and is one of the few domestic manufacturers with independent technology and production strength. The A12 developed by SEMISHARE is a 12-inch (8-inch compatible) mass production fully automatic wafer probe station. The equipment can be combined with different types of Parametric and ATE test units. Precise contact between them to complete wafer WAT/CP testing. The equipment is easy to operate and has good mechanical stability. It can provide customers with a cost-effective and high-yield wafer testing solution to meet the requirements of (fabs, Packaging and testing plants, testing plants) and other test requirements of different customers.
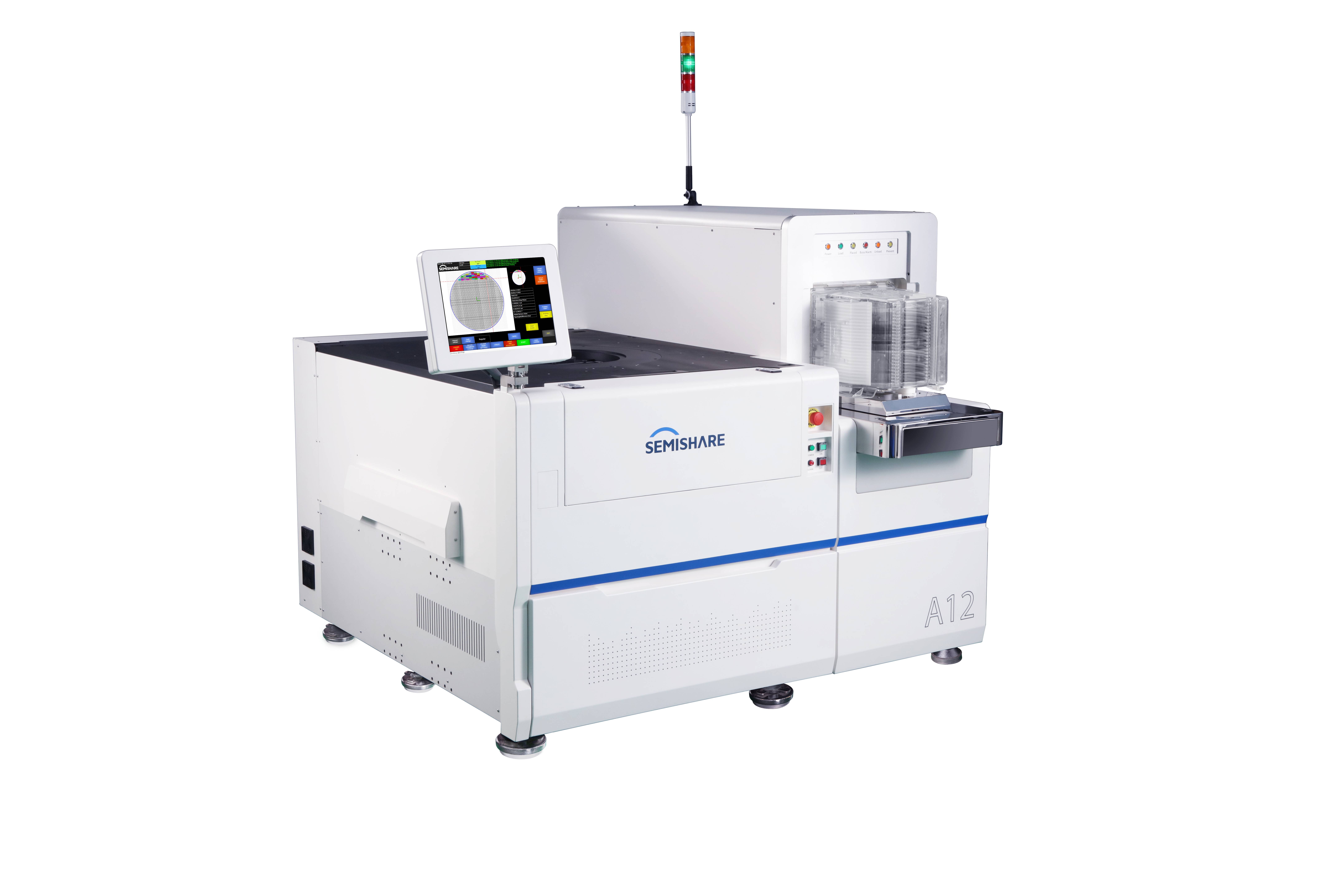
Self-developed software, simple and easy to operate, can realize 7×24 hours unattended
The self-developed software system has strong compatibility, powerful functions and simple operation, which is very friendly to novice operators. The measurement job can be put into operation at night or on weekends. Through high-resolution and high-precision temperature control, all devices on the wafer can be tested at different temperatures without operator intervention. If the probe deviates from the state of alignment with the Pad, the system will automatically realign them to save test time. It has a powerful Wafermap editing function and supports offline and file import and export functions.
Vision automatic and precise calibration
In the test situation, the precise placement of the light is crucial, and the vision is automatically and precisely calibrated, which can reduce the test time from several months to a matter of minutes in some cases. The self-designed upper and lower microscope system, unique upper and lower focusing and centering optical technology, and 4 sets of 2 million pixel high-definition digital cameras, precision pneumatic upper microscope structure, ensure that the calibration and needle sticking are in the same area, and each microscope is With high and low magnification, it can meet the needs of high-precision alignment and needle point recognition.
High strength and low center of gravity design structure, high precision and test speed, greatly improve test efficiency
Multi-directional environmental monitoring and compensation functions to solve the position accuracy changes caused by temperature and humidity changes.High-precision XYZR four-dimensional platform, XYZ accuracy up to ±1μm, R accuracy up to 0.0001°, 0.1μm resolution grating ruler, to ensure ultra-high precision motion performance. The machine frame with integrated casting and long-term aging treatment can realize 7×24 hours of uninterrupted work. The movement rate of the XY axis can reach 200mm/s, which greatly improves the test efficiency.
The core of realizing accurate, fast and automated wafer testing is to enable our equipment to operate autonomously according to the set requirements through continuous innovation of software and hardware technologies, to achieve more precise contact and shorten the time of data acquisition. SEMISHARE has been committed to provide our customers with professional test and measurement solutions.